The Process from Design to Delivery
The New Customer Process is an easy step-by-step-system. All that is required is the following:
Step 1
Submit an electronic file of your part design (2D or 3D drawing, CAD file). Underwood will review and discuss the best tooling design to manufacture your part.
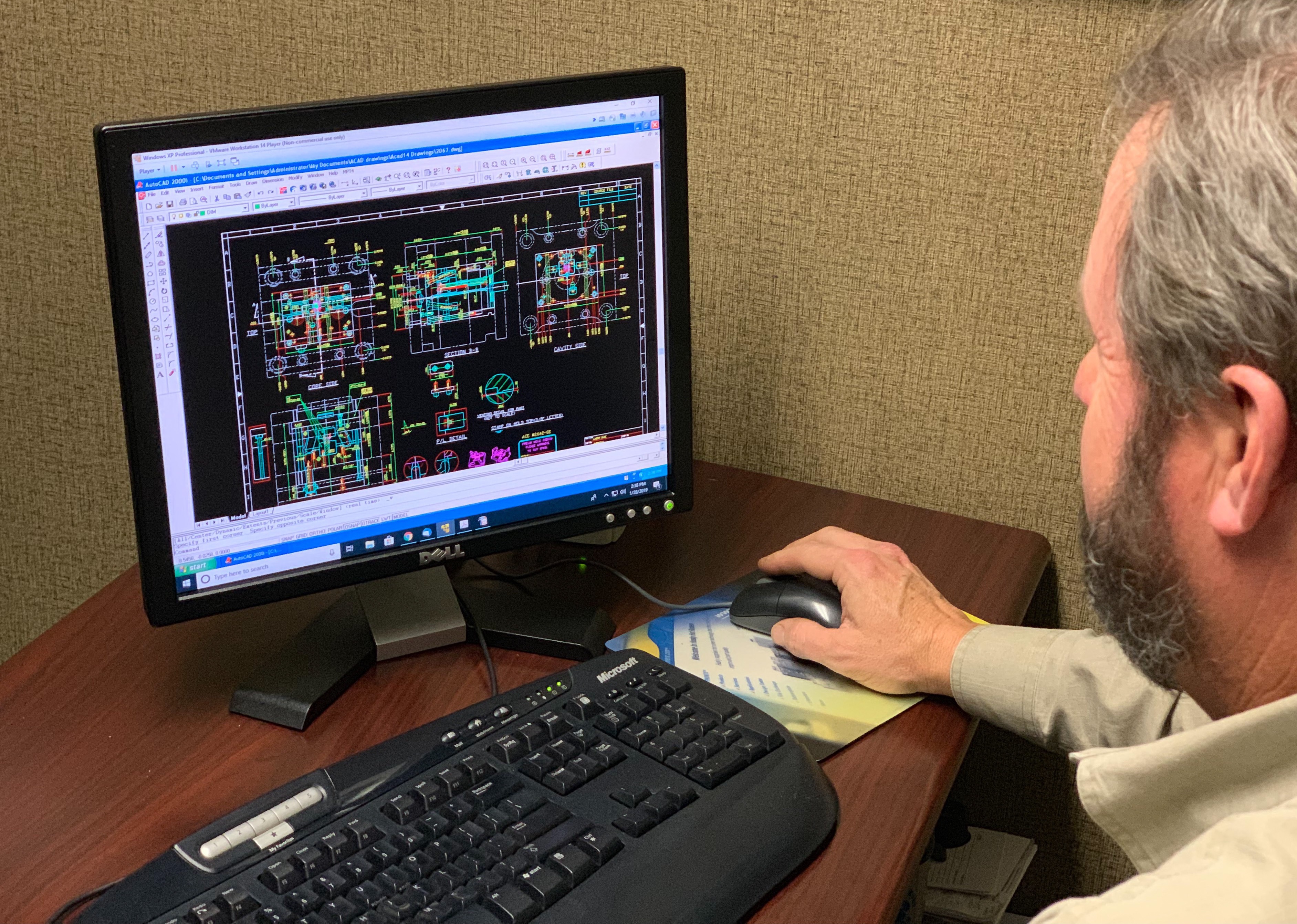
Step 2
Provide information about your project –
- Cavitation based on EAU (estimated annual usage)
- Required resin
- Mold sprue and gate design
- Secondary operations after molding
- Primary use of the product
- Quality requirements, ie., critical dimension, visuals, etc.
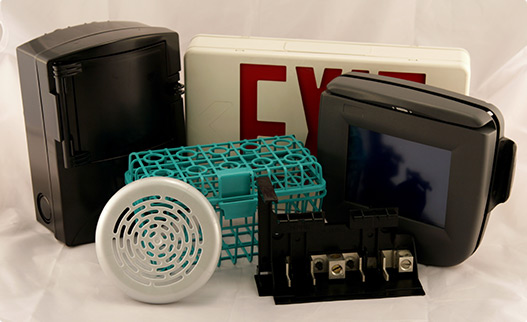
Step 3
Quoting process – you will receive a formal quote on your new tool and piece part price. Once the quote is accepted and approved, the mold fabricating process can begin. Average time-line: quotation process – 5 business days; tool fabrication – 8 to 10 weeks.
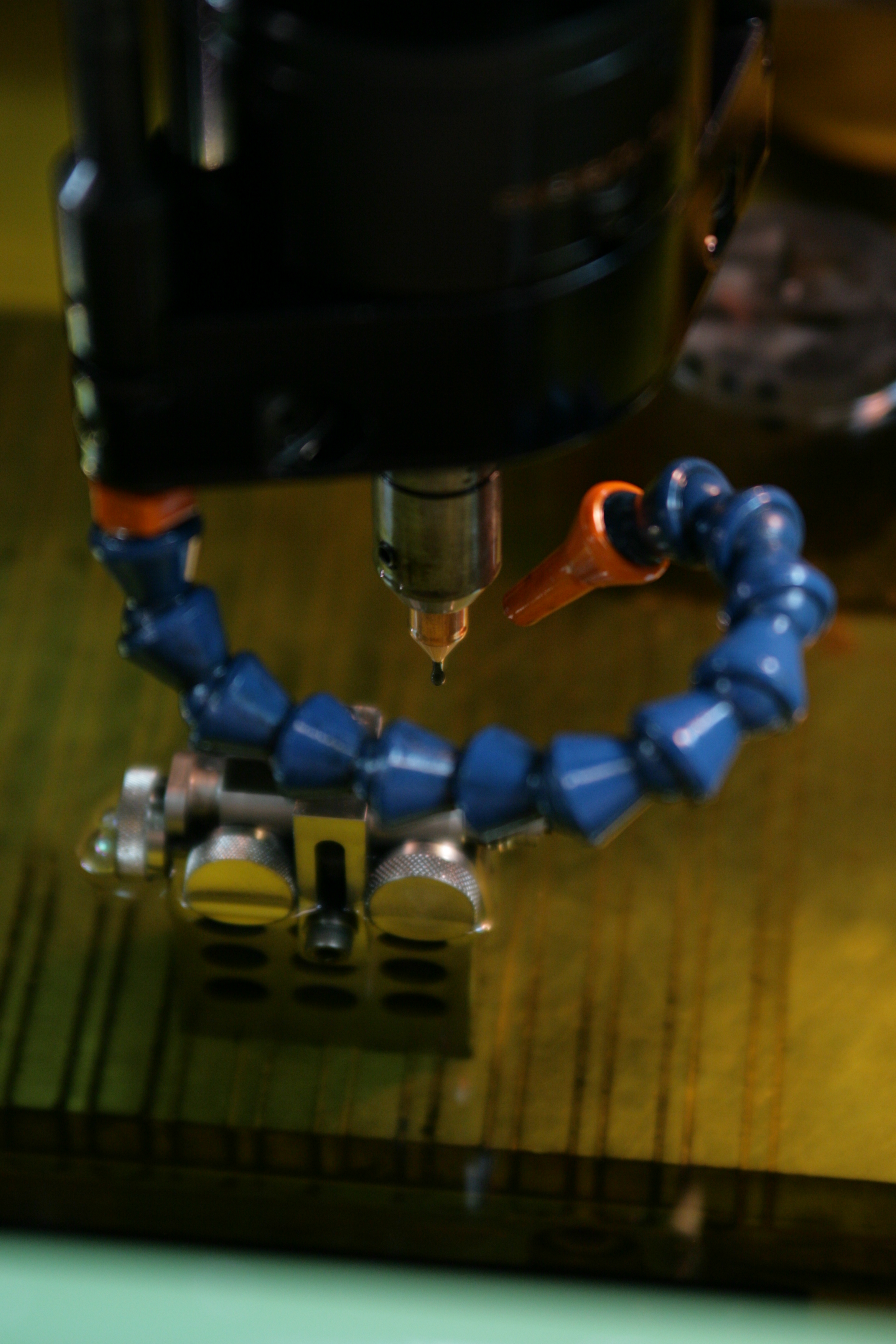
Step 4
Progress status updates – Underwood will keep you informed during interval stages of the tooling fabrication process, from start until the first shot samples are produced from the new mold. At this time first article inspections (FAI) and any requested quality functional inspections will be performed on your parts.
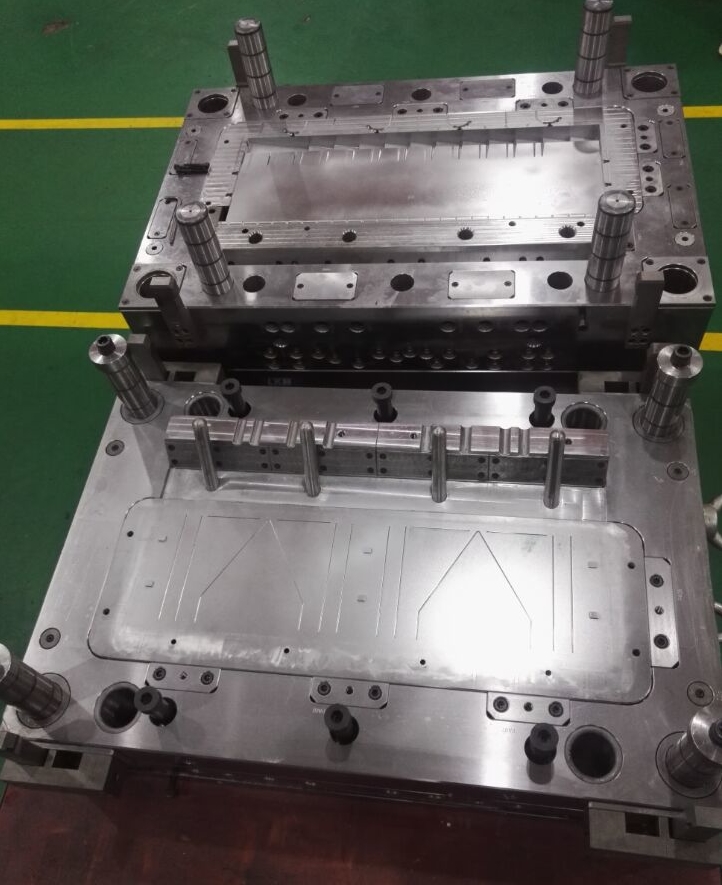
Step 5
Tool released for production – Once the initial first shot samples are reviewed and approved, the tool is released to production. Upon receipt of your purchase order (PO), Underwood will schedule the initial production run and provide an order acknowledgment.

Step 6
Your parts are packaged and delivered based on the quality requirements received in step 2 and shipping instructions documented on your purchase order.
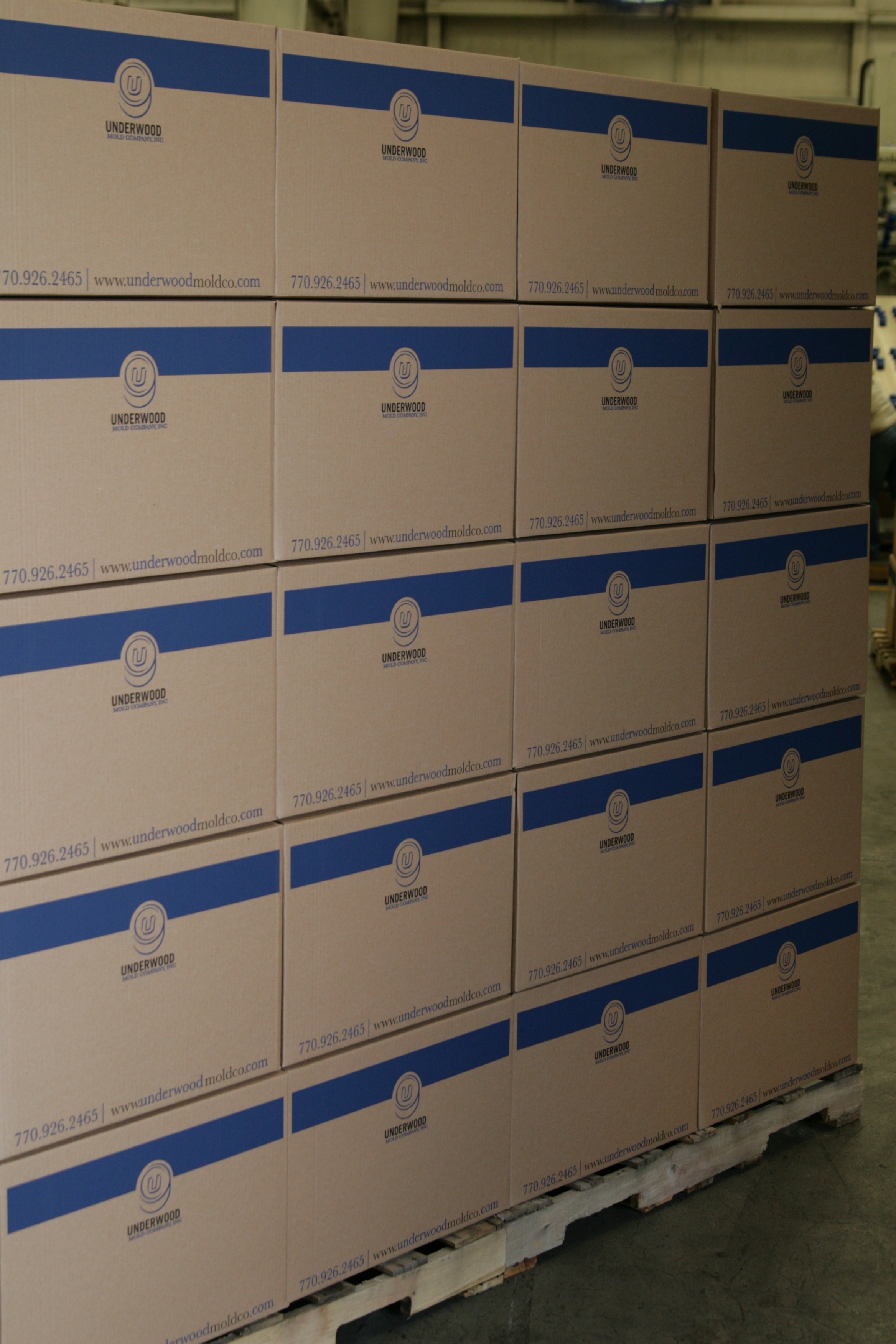
All quality records will be maintained for a minimum of 2 years unless otherwise specified and records are available upon request.